Качество сварного шва двух труб определяет срок службы всего трубопровода. Для предотвращения аварий во время работы конструкций проводят проверку трубопроводов на наличие дефектов. Такая проверка особенно важна для магистралей, проложенных под землей.
Общие сведения
Несколько способов выявляют дефекты в сварных швах труб.
- магнитный;
- акустический;
- электрический;
- оптический.
Цель — установить герметичность соединений, прочность металла в сварных швах, наличие напряжений и другие показатели, влияющие на надёжность трубопроводов. Методы дефектоскопии при этом почти идентичны для разных типов магистралей: тепловых, газовых, водо-, нефтепроводов.
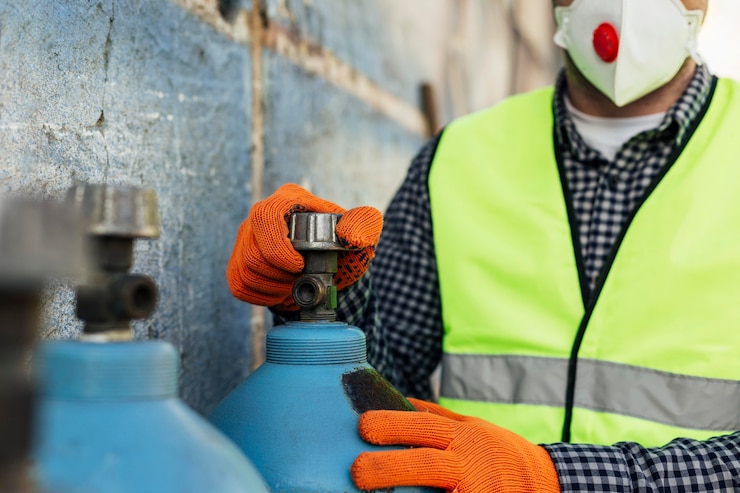
Все упомянутые способы относятся к разряду неразрушающих технологий. Дефектоскопия выполняется непосредственно на стройплощадке. Трубные стыки остаются целыми, благодаря чему уменьшаются затраты на монтаж.
Дефектоскопия трубопроводов основана на работе специального сканера – дефектоскопа. Каждая технология использует его по-своему. Среди самых эффективных –
- вихретоковые;
- ультразвуковые;
- магнитно-порошковые;
- капиллярные.
Подробно о способах
После монтажа трубопровода необходимо провести дефектоскопию для предотвращения его разрушения при эксплуатации. Дефектоскопия позволяет обнаружить все дефекты труб. Принцип работы сканеров, применяемых в диагностике, различается, поэтому следует подробно изучить каждый тип.
Вихретоковые дефектоскопы
Прибор функционирует благодаря возбуждению вихревых токов, перемещающихся от наружной поверхности трубопровода к внутренней через сварной шов. Ток, проходящий по однородному металлу, не меняет свои характеристики. В случае дефектов в шве, нарушающих его однородность, увеличивается сопротивление, что приводит к ослаблению вихревого тока.
Дефектоскоп фиксирует и расшифровывает снижение, определяя качество металла шва, дефекты и неоднородности.
Плюсы метода:
- высокая скорость проведения работ;
- низкая погрешность результата;
- невысокая стоимость проводимых операций.
Минусы:
- толщина исследуемого шва – не больше 2 мм;
- надежность прибора низкая.
Ультразвуковые дефектоскопы
Ультразвуковое исследование труб является самым распространенным методом контроля качества.
- Эхо-импульсный метод.
- Теневой.
- Эхо-зеркальный.
- Зеркально-теневой.
- Дельта метод.
Прибор направляет ультразвуковой импульс через сварной шов. В случае дефектов внутри металла, импульс отражается как эхо и возвращается обратно к прибору. Время возвращения измеряет прибор, что позволяет определить глубину расположения раковин или пор.
При втором методе применяют не только устройство для подачи ультразвукового сигнала, но и отражатель, помещенный на другой стороне сварного шва трубопровода. Зная расстояние между частями прибора и время распространения звука, можно определить местоположение и размеры дефекта при изменении второго параметра (увеличения времени).
Третий способ ультразвуковой проверки аналогичен первому. К прибору подключают отражатель, который размещают сверху на сварке, как и излучатель сигнала. Оба элемента устанавливаются параллельно друг другу. Приемник сигнала свидетельствует о наличии дефекта внутри металла, отразившего луч.
Следующий способ схож с предыдущим, но различие заключается в том, что сигнализатор и отражатель установлены под прямым углом.
Пятый способ ультразвуковой дефектоскопии встречается нечасто. Затруднения вызывает настройка аппаратуры и интерпретация полученной информации. Суть метода – изменение направленности ультразвуковой волны при ее отражении от дефектов сварных швов.
В процессе формирования луч перемещается поперек, преобразуясь в продольный. Некоторое отражение происходит симметрично.
Отражатель улавливает именно продольный сигнал; его интенсивность определяет размер дефекта в стали.
Магнитно-порошковые дефектоскопы
Принцип работы этой дефектоскопии основан на способности стали изменять магнитное поле вокруг участков с низкой плотностью по сравнению с основной массой. В местах трещин, раковин или пор магнитное поле ослабевает из-за наличия воздуха внутри металла.
Для выявления дефектов в трубопроводах используют магнитный порошок, также известный как ферромагнитное вещество. Его насыпают на сварной шов и подают электрический ток с помощью двух катушек: намагничивающей и дополнительной. Электричество внутри металла создает магнитное поле. При наличии дефектов поле вокруг них ослабевает, что приводит к притягиванию магнитного порошка.
Образующийся во время исследования на поверхности порошок свидетельствует о наличии дефекта в месте сварки этого участка. Внутренняя дефектоскопия магистральных трубопроводов выполняется данным методом.
Проверку можно провести двумя способами: сухим и мокрым. При первом использовании магнитного порошка, а при втором – водный раствор из этого порошка.
Для достижения высокого качества проверки посредством второго варианта исследуемую поверхность следует предварительно обработать промежуточным материалом: техническим маслом, солидолом и подобными ему средствами.
Магнитно-порошковая дефектоскопия обладает следующими достоинствами:
- Результат, который можно увидеть невооружённым глазом.
- низкую цену.
Недостатки:
- небольшая глубина исследования – до 1,5 мм;
- Применение допускается исключительно на трубопроводах из ферромагнитных сплавов.
- сложность размагничивания крупных труб.
Капиллярные дефектоскопы
Эта технология предназначена для обнаружения малых поверхностных трещин, незаметных без специального прибора. Такая микротрещина свидетельствует о неравномерности металла в месте соединения двух частей трубы.
Процесс дефектоскопии трубопровода проводится так:
- На сварочный шов наносят пенетрант, который проникает во все микродефекты за счет капиллярности.
- Очищают обработанную поверхность от проникшего в металл вещества.
- На поверхность наносится проявитель в виде белого порошка: талька, оксида магния или другого вещества с способностью адсорбировать другие вещества.
- Проявитель удаляет из трещин пенетрант, оставляющий на поверхности белый порошок с рисунком дефектов стыка. Индикатор отчетливо проявляется под воздействием ультрафиолетовых лучей.
Данный вид контроля трубопроводов применим для выявления поверхностных повреждений металла в зоне сварки. Для обнаружения глубоких дефектов эта методика не подходит, что является её недостатком. Главным преимуществом является легкость проведения.
Итоги
Для проверки стыков труб в магистральных трубопроводах можно применять различные методы дефектоскопии.
Каждый участок можно обследовать подходящим вариантом. При выборе оптимального метода необходимо оценить его соответствие типу стыка. Например, для водопроводов применим капиллярный метод, для нефте- и газопроводов только ультразвуковой.
Дефектоскопия трубопроводов – важная процедура для оценки качества магистрали и выявления дефектов. Проводится она различными методами. Рекомендуется проводить её на этапе монтажа, чтобы избежать проблем с протечками или разрывами после завершения работ.
Какой метод вам больше нравится, и почему? Расскажите об этом в комментариях. Поделитесь статьей в соцсетях и сохраните её в закладках, чтобы не упустить важную информацию.
Рекомендуем обратить внимание на видео, связанные с нашей темой.
Обследование прямолинейных участков магистральных труб.
Как проводится рентгеновский контроль сварных швов в производственной обстановке?